Home » Iron Oxide Pigment
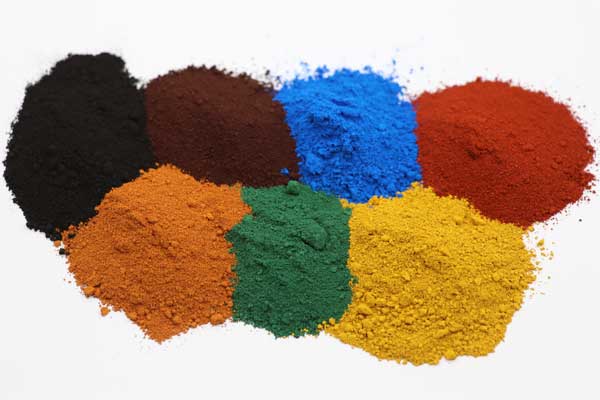
What Is Iron Oxide Pigment
- CAS NO.: 1309-37-1
- HS Code: 28211000
- MF: Fe2O3
- Color: Red, Black, Brown, Yellow, Green, Orange, Blue
Iron oxide pigment is the second largest inorganic pigment after titanium dioxide and the first largest colored inorganic pigment. It mainly ccontains red iron oxide, yellow iron oxide, black iron oxide and brown iron oxide pigment with iron oxide as the basic substance. In addition, of all the iron oxide pigment consumed, more than 70% are prepared by chemical synthesis methods, called synthetic iron oxide, such as, green iron oxide, etc… We can supply iron oxide pigments in a variety of colors. Browse the below products to look for the pigments you need and contact us if you need help. We will help you choose the right iron oxide pigments for your unique requirements.
High coloring power and high hiding power.
Excellent light resistance, weather resistance.
High temperature resistance, Strong coloring force.
Would like The Quotation?
Leave your demands in detail here(including the model, package, brand, quantity), we will reply you quickly.
Iron oxide pigments with different colors can be added in concrete to make it more attractive, improve its performance ate the same time. Choose the color you need and contact for details now.
Iron oxide pigments are widely used in coatings, paints and inks because they are non-toxic, non-bleeding, low cost, and can form a variety of different tones. Get the best price now.
In addition to make the colors of plastic and rubber more beautiful, iron oxide pigments for plastic and rubber plays a great role in preventing rubber and plastic from aging.
Would like The Quotation?
Leave your demands in detail here(including the model, package, brand, quantity), we will reply you quickly.
Know More About Iron Oxide Powder
- Application
- Features
- Production Process
Iron Oixe Pigment Uses
- As inorganic pigment, it is used for coloring of paint, rubber, plastic, construction, etc… Used as anti-rust pigment in coating industry. Used as colorant for artificial marble, ground terrazzo, colorant and filler for plastic, asbestos, artificial leather, leather polish, etc. It is also polishing agent for precision instruments, optical glass, and raw materials for manufacturing ferrite components of magnetic materials, etc…
- As the magnetic raw materials, it can be used in the electronics industry, communication equipment, televisions, computers, as well as line output transformer, switching power supply and ferrite magnetic core.
- Used in analytical reagents, catalysts and polishing agents, also used as a pigment ingredient.
- Used for coloring the outer sugar coating of various pills.
- Used as magnetic material, pigment and preparation of reducing agent, polishing agent, catalyst, etc…
- Used as a pigment for anti-paint. Because the mica iron oxide anti-rust made by this product has good water permeability resistance and excellent anti-rust performance, it can replace red lead.
- Synthetic iron oxide has the characteristics of high purity, uniform and tidy particle size, and wide chromatography. Meanwhile, varieties of colors, low price, non-toxic, as well as excellent coloring are also reasons why it has wide applications. In addition, it has the ability to absorb ultraviolet rays. All the excellent performances make it widely used in construction materials, coatings, plastics, electronics, medicine, rubber, ceramics, inks, magnetic materials, paper making and other fields.
Introduction of Iron Oxide Pigments for Concrete
As the man-made pigments from natural elements, iron oxide pigment has much stronger tinting strength and hiding power. Meanwhile, it also has excellent light resistance and weather resistance. As a result, it is the only colorant that can withstand the extreme alkaline environment of concrete without fading or leaching. So they are an excellent choice for concrete and stucco.
Iron oxide particles used in the construction industry are 10 times finer than cement particles. When adding it to concrete mixture, the iron oxide pigment particles actually surround and cover the cement particles, thereby achieving the purpose of coloring.
However, not all iron oxides have the same coloring power. Different production processes will not only affect the color strength, but also dilute or reduce the tinting intensity of pigments when adding inert filler in mixed color. In order to ensure strong coloring power of iron oxide powed, you’d better know about the production processes.
Introduction of Iron Oxide Powder for Paintings
Iron oxide pigment has characteristics of non-toxic, non-bleeding, low cost. In addition, it has the ability to form a variety of different shades. So it is widely used in coatings, paints and inks.
Iron oxide pigments are suitable for coloring of various coatings, including water-based paints, powder coatings.
Used in paints including epoxy resin, alkyd, amino and various primers and paints, as well as toy paint, decorative paint, furniture paint, electrophoretic paint and enamel.
In addition, red iron oxide primer has the function of anti-rust, which can replace expensive red lead paint, saving non-ferrous metals.
What Are Properties And Advantages of Iron Oxide Pigment
- High chemical stability and physical endurance.
- Alkali resistance. It is very stable to any concentration of alkalis and other types of alkaline materials, especially cement and lime mortar commonly used in construction, and won’t powder or affect the strength of cement building components.
- Acid resistance. It has certain resistance to general weak acids and dilute acids, but it can also dissolve in strong acids, especially when heated and concentrated.
- Light fastness. Color invariable under intense sunlight exposure.
- Heat resistance. It is stable within a certain temperature limit, and the color will start to change beyond its temperature limit. As the temperature increases, the degree of change will become more and more significant.
- Weather resistance. It isn’t affected by climatic conditions, such as, cold, hot, dry and wet atmosphere.
- Dirty air resistance. It is very stable in any dirty gas, such as, hydrogen sulfide, carbon oxide, sulfur oxide, hydrogen chloride, nitrogen oxide and other gases.
- Water, oil, solvent resistance permeability. Insoluble in water, various mineral oils, vegetable oils and ethers, esters, ketones and other organic solvents, and no penetration.
- Bright and clear color and unique hue. The color of iron oxide pigments is very clear and pure, and it doesn’t need to be embellished with other organic or inorganic pigments.
- Excellent economic effect. The iron oxide pigment has a high coloring power, fine and uniform particle size, which ensures its use value, coupled with a lower selling price, which can ensure the economic effect of the users.
Production Process of Iron Oxide
The production methods of iron oxide are mainly divided into dry method and wet method. Dry method mainly includes the calcination method of green alum, the calcination method of iron yellow, the calcination method of iron black, as well as natural iron oxide mineral ultrafine crushing method using hematite as raw material. Wet process mainly includes sulfate method, nitrate method and mixed acid method. According to the different neutralizer used in the two-step oxidation process, it can also be divided into iron sheet method and ammonia method.
Advantages. The production process is simple. Technological process is short. Equipment investment is relatively small.
Disadvantages. Quality is a little poor. It will produce harmful gases in the calcination process, which has a significant impact on the environment. For example, it will produce a large amount of sulfur-containing gas during the calcination process of iron alum. In recent years, based on the comprehensive utilization of iron-containing wastes, dry processes such as sulfuric acid cinder method, iron ore powder acidification roasting method have appeared. These methods are simple in technology and low in investment, but the quality of products is low. So they are only suitable for use in low-end fields.
Wet Process
The wet process uses ferrous sulfate or ferrous nitrate, ferric sulfate and ferric nitrate as raw materials. It first prepares seed crystal and then oxidizes to prepare red iron oxide. The raw materials can be either ferrous sulfate or ferrous nitrate solid raw material. Also can be queous solution containing ferrous sulfate, ferrous nitrate, iron sulfate, iron nitrate. The neutralizer used can be either iron sheet, iron filings or alkali, ammonia.
In recent years, based on the comprehensive utilization of industrial waste, there appears a new method. It uses titanium dioxide by-product ferrous sulfate or ferric sulfate solution, and steel plant pickling waste acid or waste water as raw materials. The neutralizing solution used is still iron scale, iron filings, alkali or ammonia.
Advantages. Produced products have excellent quality and performance. It can prepare different series of iron oxide products.
Disadvantages. The process flow is long. Consumption in the production process is high. It will generate large amount of acid waste water. And currently there is a lack of effective comprehensive utilization of acid waste water.
Sulfuric Acid Process
Take ferrous sulfate, iron sulfate heptahydrate, waste acid containing ferrous sulfate or iron sulfate, and aqueous solution as raw materials. Firstly, purity the iron salt or iron salt solution to remove impurities. Then prepare the crystal seed with sodium hydroxide or ammonia as the neutralizing agent under strict control the process conditions.
Transfer the prepared crystallization nucleus to a two-step oxidation synthesis reactor. The process conditions are strictly controlled under heating conditions. Add sodium hydroxide or ammonia to adjust the PH value of the system. And then the air is passed through for oxidation to obtain seed crystals.
Transfer the prepared qualified seed crystals to the oxidation synthesis reactor. Adjust the PH value and temperature conditions. Add iron or iron filings to neutralize the acid generated in the oxidation process. Carry out oxidation reaction through the air. And add the iron salt solution continuously during the oxidation process.
When the color of the reaction system reaches the target color standard, stop the reaction and separate the iron oxide products by filtration. The mother liquor produced by separation is acidic wastewater containing sodium sulfate.
The obvious disadvantage of this process is that it will produce a large amount of acid wastewater. And there is no reliable control and recycling method.
Nitric Acid Process
The basic principle is the same as the sulfuric acid process. Difference is that the iron salt used is nitrate. Advantage is that the quality of product obtained is better than the sulfuric acid method.
Disadvantages. The production cost is high. It will produce harmful gases and a large amount of acid wastewater in the production process. Acid wastewater contains a large amount of nitrate. And there is currently no reliable comprehensive utilization way.
Mixed acid process
Firstly, prepare ferrous sulfate solution and ferrous nitrate solution first. Then use ferrous nitrate solution as raw material, and alkali or ammonia as neutralizer to prepare seed crystal.
Transfer the seed crystal to the oxidative synthesis reactor. Adjust the temperature and PH value. Put the iron sheet or iron filings as the neutralizer, ventilate and oxidize. In the oxidation process, add ferrous sulfate and ferrous nitrate solutions to carry out the oxidation reaction.
When the color of the reaction system reaches the target color standard, stop the reaction and separate the iron oxide product by filtration. The mother liquor produced by the separation is acidic wastewater containing sulfate and nitrate.
The quality of products produced is good, which can meet the quality standards of nitric acid products. However, a large amount of acid wastewater is generated. And here is no reliable control and recycling method.
Ammonia process
The main component contained in the acidic process wastewater generated by the smmonia process is ammonium sulfate. And it is ammonium chloride when ferric chloride or ferrous chloride is used as the raw material. Since ammonium sulfate or ammonium chloride products can be recovered after wastewater treatment. There is no wastewater discharge. It is considered as a harmless and environmentally friendly production process.
However, due to the lack of research on the process and imperfect conditions for the preparation of seed crystals, which has an impact on product quality, resulting in unstable product quality. So the process is limited.
The raw material used for the production of iron oxide by the ammonia method are ferrous sulfate heptahydrate, ferric nitrate, ferrous chloride, ferric sulfate and ferric chloride crystals. They can also be waste acid, waste water containing the above iron salts or iron industrial solid waste, etc…
Disposal Measures of Waste Residue in Production
The process of producing iron oxide from sulfuric acid waste residues. In the waste residue produced, except for a small amount of impurities insoluble in sulfuric acid, it is mainly composed of unacidified ilmenite, which is discharge after treatment.
For the sludge treatment method, the plate and frame filter is generally used. With this treatment method, the recovery rate of the titanium liquid in the sedimentation process can reach 98.8%-99.0%.
The acid digested sludge from the sedimentation process enters the mud storage tank. Dilute and stir the iron oxide sludge, and then send them to the plate and fame filter by mud pump.
The liquid goes to the small-degree water storage tank. And dry the filter cake by compressed air for about 20 minutes. Then guided by a guide plate to a belt conveyor, and then manually transported to the slag yard. Use the dilute waste acid in the mud storage tank to adjust the concentration of mud residue. And use water to clean the mud storage tank.
Where to Buy Iron Oxide Powder
Chemate Technology Co.,Ltd is one of the world professional iron oxide powder manufactures and suppliers, we have been engaged in the production and export of pigment chemical products for over 15 years. Now we have formed a complete system integrating R&D, production, sales and export. As a reliable supplier, we can assure our customers.
-
Various Types
Different colors of iron oxide, the same color series with different models can meet various demands of customers. You can choose the suitable model through the color alta we show on the web, or you can provide us with your color needs, we will help you choose the most suitable model.
-
Quality Assurance
ISO9001 international quality standard system certification, ISO14001 environmental management system certification, CE certification. Strictly control every production process to ensure that it always meets the indicators. A special quality inspection department ensures that the finished product is 100% qualified.
-
Reasonable Price
The price will flutuate according to the price of raw materials and other factors. What we can guarantee is that our price always competitive in the same industry.
-
Excellent Pre-sales And After-sales Service
Would like to know more about the iron oxide for sale in our company? Inquiry us now, we will reply you as soon as we can.
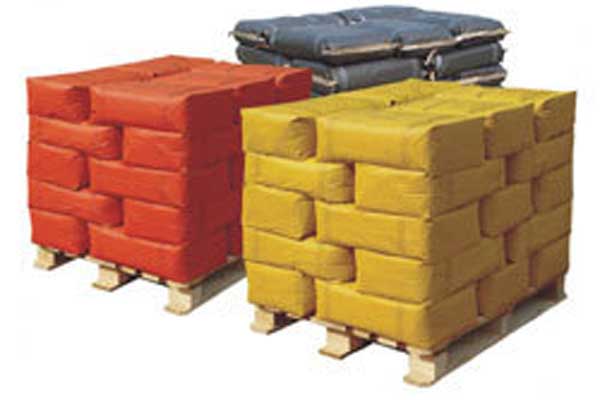
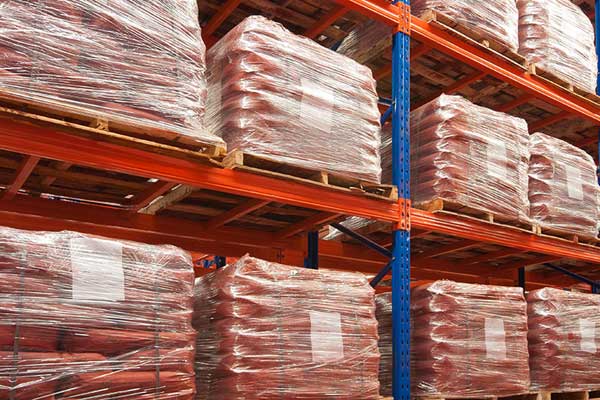

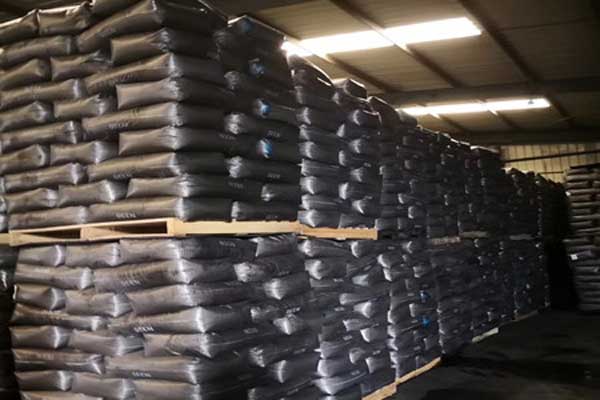

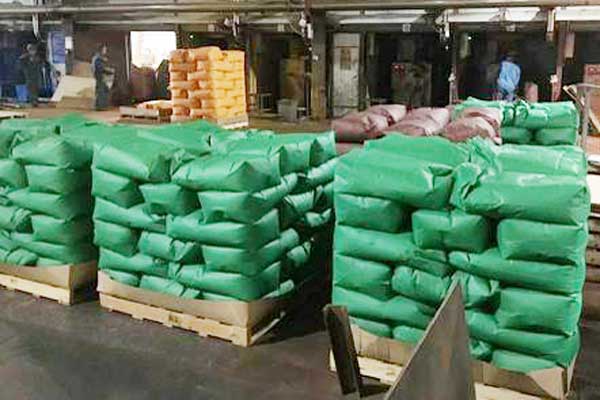
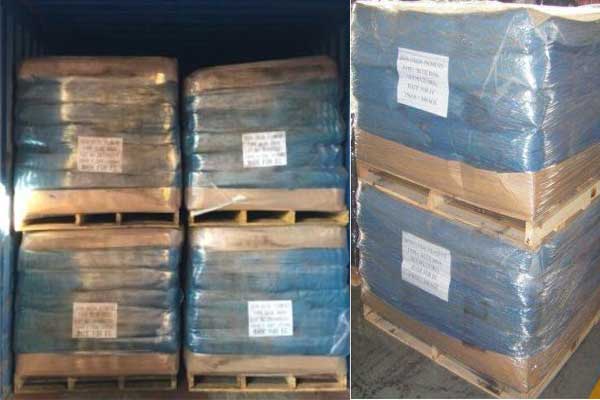
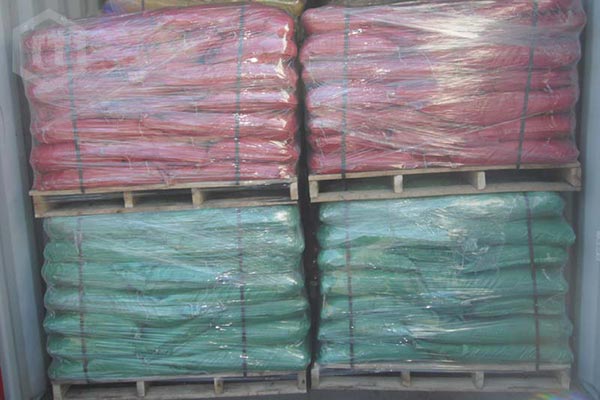
- Email: sales@chemategroup.com
- Tel: 0086-371-60921621
- Whatsapp: +86 18624832876
- Wechat: +86 18624832876
- ADD: NO.80 PUHUI ROAD,ZHENGZHOU CITY, HENAN PROVINCE, CHINA